WALBRIDGE, Ohio—Solar panels are part of any formula for fighting climate change, yet the U.S. makes few of them, since subsidized manufacturers in China dominate the market.
After years of decline, the fragile American solar industry is hoping for a turnabout bolstered by President Biden’s plans to make the U.S. electric grid carbon-free by 2035, and his insistence on a made-in-America transition that would create jobs and bolster industries deemed critical.
In seeking to “reshore” manufacturing that has moved offshore, the Biden administration is initially focusing on four industries to bolster with tax breaks or other government support. One is pharmaceuticals, whose importance the pandemic shows. The other three—semiconductors, advanced batteries and minerals crucial for electronics—are important for next-generation renewable energy. Many of the plans would require congressional approval.
At a First Solar plant in Ohio, Rochelle Wilborn runs a test to ensure each panel has enough insulation to withstand high voltage.
Solar power isn’t named as an administration priority so far, but it is lobbying for tariff or tax-law support on grounds it, too, is critical to America’s future.
The Biden administration already supports extending tax credits for solar-panel purchases and is weighing whether to back tax credits that would give domestic panel makers a lift and disadvantage imports. The administration also plans to require federal contractors to purchase many solar panels from U.S. suppliers. Changes in the tax code require Congress to sign on; administrative actions don’t.
In talking to administration officials, said
Mark Widmar,
First Solar’s chief executive, “We’ll have conversations [at the cabinet level] and they’ll say, ‘You guys are pushing an open door. We’re all in.’ ”
A White House spokeswoman wouldn’t comment on conversations but said the administration “will make investments to diversify our domestic energy sources, including solar.”
The situation of the solar-panel business illustrates some of the challenges the broader reshoring ambitions face, including divisions and conflicting interests within industries.
Solar-power manufacturers that want to build from scratch in the U.S., such as First Solar, support tariffs to fight low-price goods from abroad. But the upward pressure that tariffs put on panel prices tends to slow the adoption of solar technology and the employment of panel installers, so that many others in the industry, including solar-panel importers and companies that install panels, oppose tariffs. The different factions support different types of tax changes, too.
Tariffs “have had a detrimental impact on the solar market,” said
Abigail Ross Hopper,
president of the Solar Energy Industries Association, a trade group whose membership includes many importers and installers. “You can look at our membership all day long but the evidence shows [tariffs] haven’t worked.”
First Solar is the largest U.S.-based manufacturer of solar panels.
Reshoring the solar industry is likely to be an expensive proposition. It would require a combination of hefty subsidies through tax breaks and tariffs to burden low-price imports, according to economists and industry specialists, who say even then it’s a long shot.
“China heavily subsidizes whatever strategic industry it chooses to focus on. How does any American company ever compete?” said First Solar’s Mr. Widmar.
It would be very hard for the U.S. to be cost competitive with the Chinese, said
Kelly Sims Gallagher,
an energy professor at Tufts University’s Fletcher School who has studied China’s renewable energy policy. Still, she added: “Surely we have a fighting chance. There’s a gigantic global market.”
Some economists say the government shouldn’t be in the business of backing commercial industries. One reason is that the effort is bound to lead to a lobbying blitz by companies hunting for government backing.
Already the textile industry (protective gear) and the bicycle industry (clean transportation) are arguing that they, too, make critical goods and deserve government help.
“Once you show a lot of openness to satisfy demand for subsidies, it leads to a lot of demands that aren’t worth the government’s money,” said
Pol Antras,
a Harvard economist.
Some of the first practical cells to turn sunlight into electricity were invented in Bell Labs in New Jersey in 1954 and used to power satellites. Uses grew, and by 2000 Japan and Germany vied for leadership of a global industry. China was a small outlier.
A solar panel makes its way through the manufacturing process at a First Solar plant.
Then, local Chinese governments began backing local solar entrepreneurs with inexpensive financing and other support, competing to cash in on a growing industry. As Chinese manufacturers multiplied, prices fell sharply as a result of oversupply. Chinese companies exported excess output at prices non-Chinese panel makers couldn’t match.
China’s central government eventually stepped in to sort out the mess. It forced some solar companies into bankruptcy but kept many others alive through state financing and other subsidies. By 2011, Chinese manufacturers dominated the solar-panel industry, with about 60% of global sales, which resulted in the U.S. later imposing tariffs to block further Chinese advances.
The price decline boosted the adoption of the technology. Solar was twice as expensive as natural gas for generating electricity in 2012, but the two were comparable by 2020.
U.S. solar installations of all kinds are up 20-fold in a decade, to 19.2 gigawatts last year, according to research and consulting firm Wood Mackenzie. That is enough to power 3.7 million homes and provide 4.3% of the nation’s power needs.
More growth is projected. But few U.S. makers are left to benefit.
About half of the companies world-wide that made solar panels had left the business by 2015 as pricing pressure mounted, according to researchers at the University of Pennsylvania’s Wharton School and the Insead business school in France.
Despite a tripling of domestic solar-panel production since a 2018 imposition of broad tariffs, imports make up 85% of U.S. sales, according to Wood Mackenzie. Even First Solar now manufactures domestically just 40% of the panels its sells in the U.S., but it plans to raise that to 60% with the new factory and reach a higher percentage in the future.
First Solar’s newest plant will be in Walbridge, Ohio. It is expected to employ 500 workers and help give the region around Toledo some pizazz. “Solar is a sexy industry. It carries a lot of respect in the business community and with millennials,” said
John Gibney,
an officer of the Regional Growth Partnership, a development group.
A worker loads a machine that builds the outer frame of solar panels.
Yet even if the U.S. adds heavily to its solar-panel manufacturing, the process is now too automated to yield the wealth of higher-paying manufacturing jobs that reshoring advocates in the White House and Congress seek.
The increased U.S. output that followed the 2018 broadening of panel tariffs produced fewer than 1,000 additional U.S. manufacturing jobs before the pandemic struck, according to the SEIA. Solar-panel installation—essentially construction work—currently provides about five times as much U.S. employment as panel manufacturing.
Share Your Thoughts
Can the U.S. bring back domestic manufacturing in industries such as solar panels? Join the conversation below.
First Solar has ridden the ups and downs. After it went public in 2006, its stock price jumped eightfold. At one point in 2008 it had a larger market value than
General Motors.
Back then, First Solar’s panels produced electricity at a lower cost per megawatt than Chinese companies, which used a different technology, said
Mamun Rashid,
a former computer-chip designer who helped start a competitor, Auxin Solar Inc.
Chinese subsidies overcame the cost advantage, and by 2011 First Solar was losing money. It closed a factory in Germany, backed off plans for plants in Vietnam and France and canceled an Arizona plant for which it had already constructed the building.
First Solar, based in Tempe, Ariz., remains the largest U.S.-owned panel maker with $2.71 billion in sales last year, slightly less than it had in 2011. It has run annual losses in five of the past 10 years.
One U.S. competitor, the American subsidiary of Solar World AG of Germany, sought to fight Chinese competition through tariffs and won Obama administration backing for heavy levies on Chinese solar imports in 2012.
The tariff fight started a cat-and-mouse game that did little to help American manufacturing. To dodge the tariffs, Chinese companies shifted panel assembly for the U.S. market to Taiwan. When Washington extended its China tariffs to Taiwan in 2015, Chinese manufacturers shifted again, to Southeast Asia.
U.S. imports from Chinese-owned factories in Malaysia and Vietnam made up for a fall in China’s share. Even with tariff protection, U.S. solar production at first barely increased.
The Trump administration then doubled down on the tariff strategy. In 2018, it imposed levies on solar panels from anywhere in the world, not just China and Taiwan.
A worker secures a cable during the assembly process at First Solar.
These encouraged some U.S. investment. A Chinese company built a solar-panel factory in Florida, and a Korean company built one in Georgia. The tariffs also helped persuade First Solar, which had built its first large-scale panel plant in the Toledo area in 2000, to start work on a second sprawling factory there in 2018.
First Solar also bought enough land for a third factory, but scrapped those plans after the Trump administration weakened the tariffs in 2019 by providing exemptions for many imported solar panels.
That second plant uses glass from a factory a few miles away that heats soda ash, sand and lime to 3,000 degrees to turn them into glass slightly thinner than a window panel. The glass factory, owned by
Nippon Sheet Glass Co.
of Japan, has a furnace half the size of a football field. The finished glass is packed into crate after crate in a room so cavernous it looks like the secret government warehouse shown at the end of “Raiders of the Lost Ark.”
First Solar coats this glass with a photovoltaic film that turns sunlight into electricity. A laser etches each solar panel, dividing the coating into hundreds of solar cells. An assembly line snakes for more than a mile around a 1.1 million-square-foot building filled with furnaces, robots and computer screens.
It needs just 132 workers on each shift.
Joseph Velez,
an assembly-line worker, said a decade ago, a half-dozen people were required to trim a seal around the edge of the glass and add some components on one part of the conveyor belt. Now, only two are needed.
A solar panel starts as a single sheet of clear glass.
In now reviving its once-shelved plan for a third Ohio solar-panel plant, First Solar’s Mr. Widmar is counting on help from the White House and Congress, which are debating ways to help the industry.
Given the deep partisan divisions in Washington, that is a gamble, the 55-year-old executive acknowledges. He said he needed to make a decision now to keep his manufacturing plans on track.
The U.S. solar industry has relied for years on a rich investment tax credit, now 26% for purchasers of solar installations. Mr. Biden has urged Congress to extend the credit for 10 years.
The credit doesn’t distinguish between the use of imported solar panels and U.S.-made ones. Mr. Widmar is banking more on a proposed new tax credit that would be tied to U.S. production of renewable energy, an approach pushed by Senate Finance Committee Chairman
Ron Wyden
(D., Ore.).
Under that system, a company like First Solar, which produces domestically nearly all parts of its U.S.-manufactured panels, could get the maximum credit, while companies that assemble panels in the U.S. from foreign-made parts would get only a partial credit, and imported panels would get zero.
Linisha Parks, a worker at First Solar in Walbridge, Ohio, wraps a pallet of solar panels in bands to ensure safe delivery.
Gregory Nemet,
a University of Wisconsin solar specialist, says the Chinese successfully used a similar scheme in the early 2000s to boost their domestic wind-power industry, then dominated by European suppliers.
Mr. Widmar said he was willing to consider dropping First Solar’s support for the Trump tariffs when they expire early next year if Congress approves rich tax breaks instead. That way, taxpayers, rather than solar-equipment purchasers, would foot the bill to encourage domestic manufacturing.
First Solar CEO Mark Widmar is banking on a proposed new tax credit that would be linked to U.S. production of renewable energy.
“My customers feel like they’re being penalized because of the impact of tariffs,” he said.
Recently, Mr. Widmar added human rights to his pitch for domestic production of solar panels.
Chinese competitors rely on a technology using silicon that is frequently mined and processed in China’s remote Xinjiang region, where Beijing’s repression of the Uyghur Muslim minority is such that it amounts to genocide, according to the U.S. government. The AFL-CIO has called for banning imports of solar goods from Xinjiang, and Congress is considering legislation to do so, a move that would give a big boost to domestic production.
Beijing rejects the genocide accusation, calling it “the lie of the century.”
The Biden administration has started to press the issue internationally. On June 13, the Group of Seven wealthy democracies, at the urging of the U.S., released a statement criticizing “state-sponsored forced labour of vulnerable minorities” in the agricultural, solar and garment sectors, a statement clearly aimed at Beijing.
First Solar’s panels don’t use components made from Chinese-processed silicon. Its solar cells rely on a coating of cadmium and telluride. Recently, Mr. Widmar said, he used the issue to win a roughly $150 million contract with a buyer that had initially decided to use silicon-technology panels.
“I poked and prodded a little bit” about whether the panels might have some Xinjiang connection, he said, and prompted the buyer to rethink its supply chain.
Write to Bob Davis at bob.davis@wsj.com
Copyright ©2020 Dow Jones & Company, Inc. All Rights Reserved. 87990cbe856818d5eddac44c7b1cdeb8
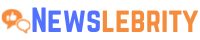